Intelligent Incident Reporting for Enhanced Worker Safety
SafetyNet is a system that comprises of a worker facing application and a manager facing dashboard, that leverages on-site event records, historical data and predictive models to intelligently identify root causes behind potentially hazardous events and suggest corrective actions for a safer, more compliant worksite.
CHALLENGE
Workers in the oil and gas industry face hazardous conditions that compromise their safety on a daily basis. Reporting and investigating incidents is time consuming and safety managers, as a result, may overlook unsafe events, which may escalate into accidents and fatalities. Due to these gaps in reporting, safety managers also cannot identify the most effective measures to mitigate and prevent on-site incidents.
OBJECTIVE
Identify underlying factors that contribute to compromised worker safety. Design and propose product strategy for an intervention which monitors the efficacy of safety training efficacy and integrates with MSA Safety's (the client) existing ecosystem.
MY ROLE
Drive user and market research, create concepts and high-fidelity prototypes, determine solution feasibility and go-to-market strategy
MSA Safety's Expertise
Being a provider of hardware, and now software, solutions for the health and safety industry since the early 1900's, MSA recently introduced the Connected Work Platform, which combines hardware and software capabilities for real-time gas detection and worker safety updates.
The safety manager is directly responsible for ensuring safety and adherence to compliance
Key stakeholders in the health and safety landscape could be broadly categorized into these categories:
REGULATORY BODIES
Establishing and enforcing safety standards to create a safe work environment
SAFETY MANAGERS
Directly responsible for developing, implementing, and overseeing safety programs
WORKERS
Influence the effectiveness of safety measures and the overall safety culture
EMPLOYERS
Allocating resources to implement best practices
What does worker safety entail?
GOING PAST THE BARE MINIMUM
by initiating a good safety culture through PPE, standards, procedures, training, identifying and reporting.
ALIGNED WITH WORKER'S INTERNAL MOTIVATIONS
by ensuring that the worker can be in good health at work to support their family
CONTEXT-SPECIFIC SAFETY MANAGEMENT
by introducing customizable safety training depend on worker and site specific needs.
UNDERSTANDING OF HUMAN ERROR
to further identify true root causes to manage workplace accidents
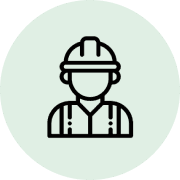
Worker's Safety Needs
PHYSICAL WELL-BEING
Workers prioritize measures that protect them from immediate physical harm. The motivation is self-preservation and the desire to return home safely to their families.
FINANCIAL STABILITY
Injuries or accidents on the job can result in costly medical bills, lost wages from missed workdays, and potentially even long-term disabilities that limit future earning potential.
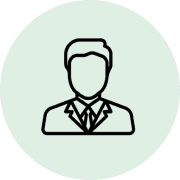
Manager's Safety Needs
LEGAL COMPLIANCE
Being compliant is an important part of a safety manager’s job, as breaking compliance is a cost to the company and a detriment to the safety managers.
COST REDUCTION
Incidents result in direct costs like medical expenses, compensation claims, and property damage, as well as indirect costs like lost productivity and increased insurance premiums.
“Twenty years ago workers were treated like iron – replaceable. My goal is to make these workers take as little risk as possible and get them home to their families.”
- Safety Manager, Oil Well Drilling Company (Pittsburgh, PA)

Fear of Repercussions
Workers tend to avoid reporting incidents due to the fear of repercussions.
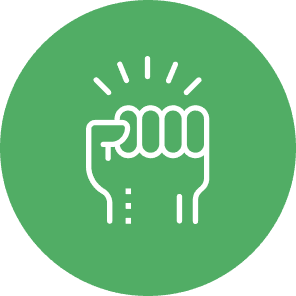
Lack of Oversight
Safety managers cannot be present at all times to witness and record every single near miss or unsafe act.
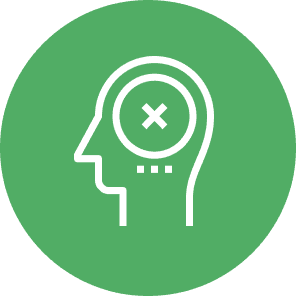
Misguided Perceptions
Some workers may not report near misses, unsafe acts, and positive observations because they seem trivial and less time critical.
Lack of data around unreported incidents results in potential escalation into serious accidents
Heinrich Triangle Theory
THE OPPORTUNITY
How might we improve visibility of hazardous events and their root cause on worksites, for a safer and more compliant site?
SafetyNet
SafetyNet collects data about unsafe events from a worker facing reportint tool and data generated from devices worn by workers. It analyzes this data with the help of historical data about the same event to share a root cause analysis and recommendations with the safety manager.
SafetyNet creates a root cause analysis for managers to investigate possible reasons and take action
Why this works:
1
Events can be visually traced to its root causes, along with recommendations
2
Every level is backed by worker and device data
3
Use of 5 Whys: A process that is reflective of industry practices
How this works:
The worker is nudged to log an event if their device detects an anomaly
Workers can report through a streamlined process, reducing the time and effort required to report, while retaining accurate detail.
The manager can view event logs and associated details for further investigation
1
FREQUENT EVENTS
Frequently logged event types are called out to highlight the need for immediate action
2
ROOT CAUSES IDENTIFIED PREVIOUSLY
Root causes from previous similar events give the manager a direction for investigation
3
HIGHLIGHTING CONSEQUENCES OF EVENTS UNADDRESSED
Data on consequences of repeated near misses to ensure prompt corrective action.
Transparent channels of communication retain trust for workers
Investigation through Data-informed event diagnosis
The manager can evaluate effectiveness of reforms over time
1
FREQUENCY OF EVENTS
Event specific trends to understand effectiveness of changes introduced
2
IDENTIFYING IMPROVEMENT AREAS
Frequent root causes are indicated for easy identification of recurring issues
Implementation Model
Existing data was studied to identify types and sources of information that can be collected and the picture it can build. Mockups of worker logs and data were broken down logically with the help of two LLMs to create a visual tree of causal analysis.